Continuous Improvement Coordinator
Rumunsko
Full time
Bachelor
2025
Are you passionate about optimizing production processes and eliminating inefficiencies?
Do you thrive in a role where you can lead lean initiatives and drive continuous improvement?
Are you ready to make a tangible impact on operational excellence?
3 times yes?
Our promises to you
- We take care of your professional development through intensive and continuous training programs.
- You will have contact with an international working environment with colleagues in different European countries.
- An attractive career perspective in a successful and growing company.
- A great team of colleagues will welcome you as if you have known them forever.
- Free transportation (you can choose to come with your own car, or the transport offered by the company).
- Meal vouchers.
- The 13th month salary is paid together with your December salary according to our internal rules.
- Schedule is from 8 am to 4:20 pm (Monday - Friday), no overtime needed.
You will be responsible for:
- Leading and executing lean production projects to enhance operational efficiency.
- Developing and implementing strategies for workplace organization, constraint management, and production flow optimization.
- Establishing and coordinating lean teams to support continuous improvement initiatives.
- Training and mentoring employees on lean methodologies and best practices.
- Conducting cost-benefit analyses and optimizing resource allocation for lean manufacturing.
- Ensuring the timely supply of produced and purchased materials to support lean processes.
You will report to the Operational Excellence Manager.
You are our missing link when you recognize yourself in the following:
- Education & Experience: Bachelor’s degree in Engineering, Industrial Management, or a related field (preferred), with prior experience in lean manufacturing, process improvement, or a similar role in a production environment.
- Technical Expertise: Strong understanding of lean manufacturing principles (5S, Kaizen, Kanban, Value Stream Mapping, One-Piece Flow, etc.), proficiency in constraint management and process optimization techniques, and the ability to conduct cost-benefit analysis and resource planning.
- Soft Skills: Strong leadership and problem-solving abilities, excellent communication and training skills, ability to work cross-functionally and influence change, and a detail-oriented, proactive, and results-driven mindset.
- Language Proficiency: Fluent in the local language and proficient in English
Selection stages:
- In case you fit the profile, you will be contacted by an HR Specialist in order to establish a first interview, on-line/by phone.
- After the first interview there will be an assessment followed by an interview with the Hiring Manager.
Join us in making continuous improvement a reality! Apply now and be a driving force in our journey towards operational excellence!
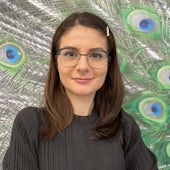